Written by Ongweoweh team member Martin Hawkins
In the post-pandemic world, companies have had to reevaluate their supply chains, their goals, and even the way they do business. Although this can be a painful process to go through, the results may yield valuable change that leads to meaningful, long-term improvements for your organization.
One of these improvements which can be realized at this time is the implementation of a repair and return pallet program. Ongweoweh has a proven track record of introducing and managing these programs for our valued customers, more and more of who are asking us about repair and return programs.
Basics of a Repair and Return Program
The simple explanation is that a repair and return program allows you to recover the pallets that you have shipped out to your customers and re-use them.
Repair and return programs are a wonderful way for a company to both save money and reduce their carbon footprint.
When a pallet needs a repair, it normally will only need 1-3 new deck boards, depending on your requirements. These repairs can be made quickly and easily by an experienced pallet professional, and the cost is therefore favorable compared to building a brand-new pallet, or even a combo or remanufactured pallet.
The carbon dioxide produced by the manufacture of 1-3 new components is also much less than the CO2 produced by building a new pallet. While transporting these repaired pallets back to your facility will expend carbon, any additional emissions are almost guaranteed to be less than the impact of building a load of new pallets.
Save Money…
To illustrate how much money a company can save by investing in a repair and return program, let’s look at a real-world example of one of Ongweoweh’s customers in the Midwest.
This particular facility only uses one pallet design and in 2023 they bought 203,300 wood pallets. They use a customized hardwood 48 x 40 with four stringer boards and a four-way entry. Their average pallet price in 2023 was $15.23, and Ongweoweh was able to offer them a price of $10.00 using a repair and recovery program. On a single load of 600 pallets, this results in $3,138.00 in savings, but the potential savings over the course of an entire year are much more impactful.
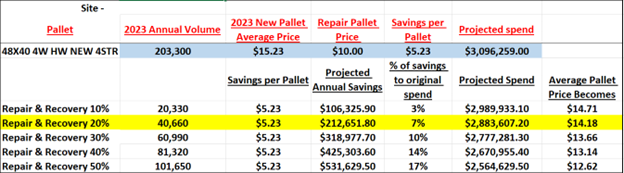
The table above shows the annual cost savings we could offer to this facility based on volume. It is worth mentioning that the potential savings are tied to how many pallets can be recovered, and how many can be repaired.
…And Save the Planet
All pallets are not created equal, so determining how much a repair and return program can reduce your company’s carbon footprint must be done on a case-by-case basis. However, to illustrate the potential impact, we can look at some basic information that we know about wood pallets.
Thanks to the EPD, we know that the manufacture of a new, standard GMA pallet produces 10.39kg of carbon dioxide. We also know that a standard GMA has 14.22 board feet of lumber, so about .73kg of CO2 is produced per board foot of lumber.
While deck boards can come in many different thicknesses and widths, we know that a standard deck board used in a GMA is 40” wide. Using a simple board footage calculation, we can say that a normal lead board is .95 board feet, and a normal interior board is .69 board feet.
In a normal repair and return program, only deck boards are replaced and if there is damage to a stringer, the pallet is retired. So, if for example a pallet needs two lead boards and one interior board for a repair, we can estimate a carbon footprint of 1.89kg of carbon dioxide for the repairs, compared with 10.39kg for a new pallet.
Of course, this assumes that new lumber will be used for repairs. When a repair and recovery pallet is retired, there are components that can still be used as repair material, which further reduces the carbon footprint of the pallet.
Thanks to Ongweoweh’s advanced, customized reporting, we can work with our customers individually to track their pallet’s carbon footprint much more accurately than the example above.
In fact, many of our customers use our reporting to show their stakeholders the positive environmental impact that their pallets and their supply chain are making. Here is an example of what an environmental KPI report from Ongweoweh can look like.
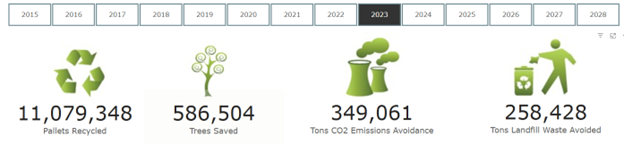
Potential Obstacles
This program seems simple and easy to implement, however, in practice, it can get tricky.
For example, how far away is your customer? Most pallet providers are small, local operations who stay within a 100-200 mile range from their mill. If your customer is outside of your pallet provider’s range of service, you will have to bring in another company to help retrieve your pallets.
If you are able to find a partner to repair and return your pallets, are they building to spec? Do they have the right repair materials at their disposal?
It may be surprising to some, but like any industry there are a few bad actors in the pallet business. These bad actors may try to build under-spec to maximize their profits. Alternatively, perhaps your pallets require kiln-dried components. What if the company you identified to do your repairs is not able to procure KD wood?
The quality of your pallets would suffer in either of these scenarios, which can potentially put your workers’ safety at risk and can cause breakage. So, how does a humble pallet user realize the advantages of a repair and return program?
First, you will need to coordinate with your customer so they are segregating your pallets from their own and from pallets sent in from other suppliers. Often times you will need to offer a rebate in order to incentivize this.
Next, you may need a local pallet company to pick up these pallets for inspection and repair. In this case, you would, need to negotiate a fair repair price, and potentially an inspection price with your selected mill.
Finally, you would need to arrange storage for your repaired pallets until a load is ready to ship.
Or, perhaps you know of a company with over 20 years of experience running successful repair and return programs for Fortune 500 companies across the country.
How Ongweoweh Can Help
Ongweoweh has been in the pallet business since 1978 and this longevity in our industry has given us a plethora of valuable relationships with local pallet suppliers. We currently work with over 1,700 suppliers in North America and Puerto Rico.
Therefore, we know exactly which pallet providers to partner with in order to seamlessly implement repair and recovery programs no matter where they are needed. Our connections don’t end with the pallet industry.
In our 45-year history, we have worked with many companies large and small, so it is possible that we have an existing relationship with your customers. So, whether we are already in contact with your customers, or their suppliers, Ongweoweh can easily recover, repair, and return your pallets.
Meanwhile, being an ISO certified company, Ongweoweh has the right processes in place to assure that our customers get the right pallet at the right price every time.
We decline to use suppliers who do not build to spec, or engage in other undesirable behavior, so you won’t have to worry about employee safety or breakage.
Our advanced reporting allows our customers to easily understand and track their environmental impact, their pallet costs, and any supply chain KPI that is important to them.
Finally, as a proud Native American MBE, any spend with Ongweoweh unlocks tier 1 diversity spend. We are also working hard to increase our own diverse spend, which can unlock tier 2 diversity spend for your company.